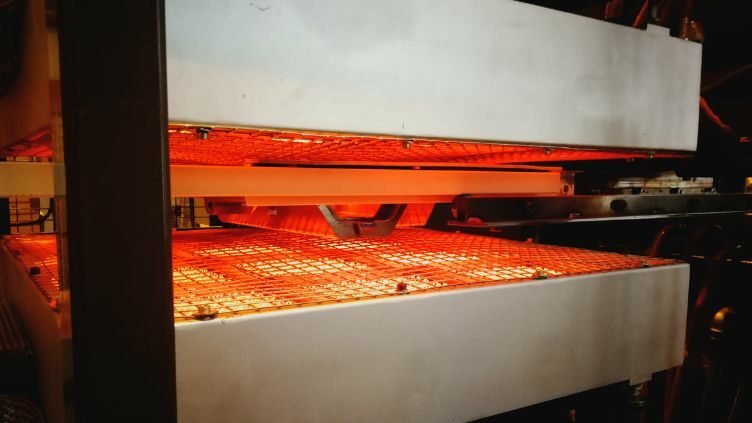
Procédé rapide de mise en œuvre composites & thermoplastique : à la découverte de la technologie FASTRAC
Composites, Procédés
Publié le : 13/01/2025 par Damien GIRAUD
La technologie brevetée Fastrac permet de produire des pièces composites à haute cadence tout en réduisant les coûts et les émissions de CO2. Elle offre des gains en productivité, flexibilité et durabilité.
La technologie Fastrac donne la possibilité d’atteindre l’un des paradigmes de l’industrie des composites : produire des pièces techniques à haute cadence tout en réduisant les émissions de CO2 et coûts associés. En effet, elle rend accessible la transformation de composites TP avec des cadences de fabrication proche de l’estampage tout en maîtrisant les performances mécaniques des pièces, limitant les couts et pertes matières et ce avec des émissions de CO2 réduites. La technologie Fastrac est brevetée et est issue d’un projet de développement. Elle permet la mise en œuvre d’organo-sheet non consolidés c’est-à-dire sous forme de tissu. Ainsi le coût matière en entrée est réduit par rapport au procédé d’estampage.
Concrètement, en quoi cela consiste ?
Le principe est le suivant :
- Préparation de la matière : Le nombre de couches de tissu nécessaires à la fabrication d’une pièce est empilé à froid entre 2 coquilles ou flasques en acier de 10mm d’épaisseur assurant une conductivité thermique optimisée. Les flasques sont fermées mécaniquement, avec ou sans vide.
- Préchauffe : L’ensemble flasque / tissu organo-sheet / flasque réalisé en étape 1 est transféré dans un moule froid sur presse. Une pression est appliquée pour contraindre le tissu à se déformer, puis si besoin une mise sous vide des tissus dans les flasques est possible notamment pour limiter l’oxydation de certaines résines TP.
- Transfert sous Infra-Rouge : L’ensemble flasques/organo-sheet est ensuite convoyé sous four IR. L’exposition aux IR dure le temps nécessaire à la fusion du TP.
- Consolidation : Lorsqu’en 3 la fusion est atteinte, l’ensemble flasques/organo-sheet est transféré dans un moule froid dont la température est différente de celle de la préchauffe. Une pression de compactage est appliquée. Après un temps de refroidissement sous pression suffisant, le moule peut être ouvert afin de libérer l’ensemble flasques/organo-sheet.
Quels sont les avantages de cette technologie ?
- La matière achetée est « prête à l’emploi ». Cette dernière est ainsi plus adaptative que les plaques consolidées utilisées en estampage. Le coût est moins élevé, les pertes sont limitées et les empilements peuvent être réalisés selon des orientations à façon. Il est aussi possible de former des pièces à matrice différentes successivement.*
- La technologie permet l’usage de matrice TP ou TD, ainsi la conversion vers une transformation SMC est possible.
- Les émissions de CO2 sont réduites par rapport à l’estampage.
- Le démoulage peut être réalisé à température basse, ainsi la pièce est manipulable immédiatement*
- Possibilité de réaliser des pièces near netshape*
- L’intégration de fonctions électroniques et/ou esthétiques est possible*
*gain de productivité
Pour quels marchés s’applique-t-elle ?
Les marchés visés par cette technologie sont l’aéronautique (pièces hors classe 1), l’automobile, le sport et loisir, le médical, etc.
Afin de découvrir la technologie et ses possibilités, rejoignez notre webinaire dédié :
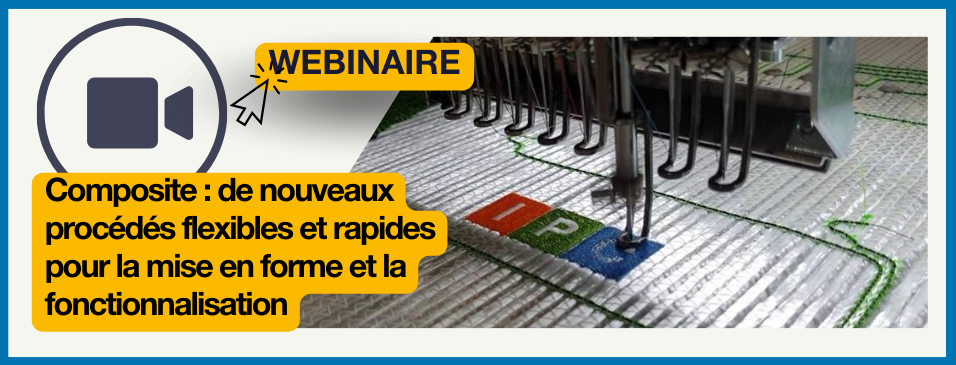